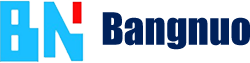
Company specializing in the production of Dagong machines, floor plate machine, guardrail plate machine, corrugated tile machine...
The Gutter Roll Forming Machine is designed to manufacture seamless metal gutters used in residential, commercial, and industrial buildings for efficient water drainage. This machine ensures precise shaping, cutting, and consistent production of durable gutter profiles. Follow these instructions for optimal operation and maintenance.
1. Pre-Operation Setup
Machine Inspection – Check the rollers, cutting system, hydraulic components, and electrical connections. Ensure all parts are secure and properly aligned.
Power & Safety Check – Connect the machine to the correct power source. Test the emergency stop function and verify that all safety guards are in place.
Material Loading – Place the metal coil (galvanized steel, aluminum, or copper) onto the decoiler. Adjust the feeding guides to ensure smooth material entry.
Material Feeding – Carefully feed the metal strip into the rollers, ensuring proper alignment to prevent deformation.
Parameter Setup – Use the control panel to enter the required gutter profile dimensions, length, and cutting parameters.
Roll Forming Process – Press Start, and the machine will gradually shape the material into the desired gutter profile. Monitor the alignment and adjust if necessary.
Cutting Mechanism – The hydraulic or mechanical cutting system will cut the gutters to the programmed length with precision. Ensure all cuts are smooth and free from burrs.
Quality Inspection – Check the finished gutters for correct dimensions, smooth edges, and uniform profile.
Shutting Down – Turn off the machine, disconnect power, and remove any metal debris from the rollers and work area.
Routine Maintenance – Lubricate moving parts, inspect rollers and cutting blades for wear, and ensure hydraulic and electrical systems are functioning correctly.
By following these steps, you ensure efficient production, high-quality gutters, and long-term machine performance.