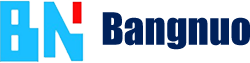
Company specializing in the production of Dagong machines, floor plate machine, guardrail plate machine, corrugated tile machine...
The Soundproof Panel Roll Forming Machine is designed to produce high-precision metal panels with perforations that reduce noise pollution. These panels are commonly used in highways, industrial zones, railways, and construction sites to block and absorb sound effectively. The machine ensures consistent shaping, perforation, and cutting, delivering high-quality, durable panels that meet industry standards.
Machine Inspection & Safety Checks
Structural Inspection: Examine rollers, cutting blades, perforation system, hydraulic components, and electrical connections to ensure they are intact and aligned correctly.
Power & Safety System Check: Connect the machine to the appropriate power supply. Test the emergency stop function, verify safety guards, and ensure there are no loose components.
Lubrication & Cleaning: Apply lubricants to the moving parts (rollers, chains, and cutting system) to prevent friction and wear. Remove any debris from previous operations.
Material Loading
Select the Material: Choose metal coils such as galvanized steel, aluminum, or stainless steel, which offer durability and corrosion resistance.
Set Up the Decoiler: Load the metal coil onto the decoiler and secure it properly to avoid misalignment during feeding.
Adjust Feeding Guides: Ensure the material is aligned correctly to prevent deformation while passing through the rollers.
Material Feeding & Calibration
Feeding the Metal Strip: Carefully insert the material into the rollers, making sure it aligns perfectly with the forming stations.
Control Panel Setup: Input required parameters such as panel dimensions (width, thickness, and length), hole perforation pattern, and cutting length. Verify settings before operation.
Roll Forming Process
Start the Machine: Press Start, and the rollers will gradually shape the metal into the soundproof panel profile. The forming stations apply even pressure to ensure uniform shaping.
Monitor & Adjust: Check the panel’s progress through the machine. Adjust alignment settings if necessary to prevent warping or uneven forming.
Perforation & Cutting
Perforation Process: The automated perforation system punches holes into the panels at predetermined intervals to enhance sound absorption. Ensure perforation patterns match the required noise reduction standards.
Precision Cutting: The hydraulic cutting system trims the panels to the specified length with smooth edges, preventing material waste. Check the cutting system for accuracy and burr-free results.
Quality Inspection
Dimension & Perforation Check: Measure panel width, length, and perforation hole alignment to ensure compliance with design specifications.
Surface Finish Inspection: Ensure there are no burrs, dents, or rough edges. If necessary, perform edge smoothing for a polished finish.
Shutdown Procedure
Turn Off the Machine: Power down the system and disconnect it from the electrical source.
Remove Debris: Clean metal shavings and residual dust from rollers, the perforation unit, and the cutting section.
Lubrication & Component Check: Apply lubrication to moving parts, inspect rollers for wear, and verify that the cutting blades remain sharp for the next production cycle.
Daily Maintenance
✅ Inspect rollers for alignment and wear.
✅ Clean dust and debris from the perforation and cutting sections.
✅ Test emergency stop and safety features.
Weekly Maintenance
✅ Check and tighten bolts, nuts, and fasteners.
✅ Inspect hydraulic and pneumatic systems for leaks.
✅ Lubricate all moving components for smooth operation.
Troubleshooting Common Issues
Uneven Panel Shape? Check roller alignment and adjust pressure settings.
Misaligned Perforations? Verify punch die settings and ensure material is properly fed.
Rough or Incomplete Cuts? Inspect the cutting blade and sharpen or replace it if necessary.
Following these steps will ensure efficient production of high-quality soundproof panels while maximizing machine lifespan and reducing downtime. By maintaining precision in forming, perforation, and cutting, this machine supports industries in reducing noise pollution effectively.