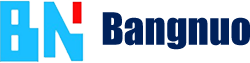
Company specializing in the production of Dagong machines, floor plate machine, guardrail plate machine, corrugated tile machine...
The Shelf Beam Roll Forming Machine is designed to manufacture high-strength shelf beams used in storage racks and warehouse shelving systems. It automates the forming, punching, and cutting processes, ensuring precision and efficiency. Follow these step-by-step instructions for safe operation and optimal performance.
1. Setup & Preparation
Machine Inspection – Check rollers, fasteners, cutting blades, and electrical connections. Ensure all components are aligned and free of damage.
Power & Safety Check – Connect the machine to the correct power supply. Verify that emergency stop functions and safety guards are operational.
Material Loading – Place the steel coil (galvanized/cold-rolled steel) onto the decoiler. Adjust the feeding guides for smooth and centered material entry.
Material Feeding – Gradually feed the steel strip into the machine while keeping it properly aligned to prevent deformities.
Parameter Setup – Use the control panel to set the beam length, hole positioning, and bending specifications. Double-check the settings before starting.
Roll Forming Process – Press Start, and the rollers will progressively shape the material into shelf beams. Monitor alignment and adjust if needed.
Punching & Cutting – The automated punching system creates holes for assembly, and the hydraulic cutter trims beams to the programmed length. Ensure clean and precise cuts.
Quality Inspection – Examine the finished beams for dimensional accuracy, smooth edges, and precise hole placement.
Proper Shutdown – Stop the machine, disconnect power, and clean the working area to remove debris.
Routine Maintenance – Lubricate moving parts, check rollers and blades for wear, and inspect hydraulic and electrical systems regularly for consistent performance.
By following these steps, you ensure smooth production, high-quality output, and the longevity of your Shelf Beam Roll Forming Machine.